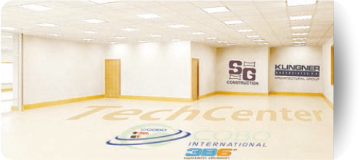
Cobo takes ambitious steps
from "The Hawk Eye" Newspaper / March 2014
Italian firm will add tech center, products to Burlington facility.By REX L. TROUTE
Cobo International built its 30,000-square-foot manufacturing facility in Burlington in 2003, added a 20,000-square-foot logistics center at 401 S. Roosevelt Ave. in 2010 and will add a tech center this year. The 8,000-square-foot tech center will be constructed inside the manufacturing plant and on top of the existing offices, creating an interior second floor. The new space will consist of two rooms — an operations room for training employees and an engineering room where a mechatronic system is implemented. Mechatronics is a design process that includes a combination of mechanical engineering, electrical engineering, telecommunications engineering, control engineering and computer engineering. Cobo International will use the mechatronic system to create new products, work on products being transferred in and develop its own software for certain products. Mainardi said in order for its products to stay on top in the construction industry, the mechatronic system will help Cobo retain its competitiveness and high quality. With vehicles and equipment in the construction industry involving more electronic control, Cobo decided to advance to the next generation of technology. "We would like to create herein Burlington added value," Mainardi said. "We have invested in a lot of technology." The company will be looking to hire more engineers for the tech center. S G Construction Co. of Burlington will build the addition, with construction scheduled to start any day and be completed by June.
One of the products to benefit from the design work in the new tech center will be a steering column, which is called a plug-and-play component. Rather than a company like Caterpillar, one of Cobo's customers, spend time piecing together 100 parts to make one steering column, Cobo can do it for them. Then all Caterpillar will have to do is install the steering column into the appropriate piece of equipment. Cobo is about two years away from completing a steering column for a Caterpillar paver. Cobo has been making the steering columns in a plant in Italy, but wants to transfer the work to the Burlington plant this year. Several companies in the U.S. that will use Cobo plug-and-play steering columns are Case New Holland (combines); Terex in Waverly (cranes); Gehl/Manitou Americas in West Bend, Wis. (wheel loaders) and Grove in Manitowoc, Wis. (lifts and material handlers). When Cobo gets the steering column line up and running, it most likely can manufacture 5,000 units per year, said Massimiliano Ruzzi, the Burlington plant manager. The plant also will add plastic molding capabilities to the steering column line, Ruzzi said. "This is the future," Mainardi said. The steering column line could add 15 to 20 employees to the manufacturing floor. Cobo International's workforce at Burlington's plant has 120 employees split between two shifts, and three employees working at the logistics center.
He cited a partnership Cobo has with Excavating Solutions in Noblesville, Ind. Cobo created a product, Canview 3, which serves as an x-ray machine of sorts for an excavator — identifying underground pipes. The operator of the excavator can work off the display screen of the Canview 3 and dig around the pipes without looking at the ground. Another advance in technology Cobo is working on is called connectivity. "All the parts have to communicate," Mainardi said. Cobo is creating the next generation of sensor, which can be placed on every piece of farm equipment, such as tractors, planters, etc. An iPhone can be used as a bridge between the sensors and a computer server, where information is collected from work being done in the field. The technology already is being used in Europe, and Cobo wants to bring it to the U.S. "We are very ambitious," Mainardi said. Cobo started making cable reels for cranes at the Burlington facility about two or three months ago. One cable reel can weigh up to 200 pounds.
|